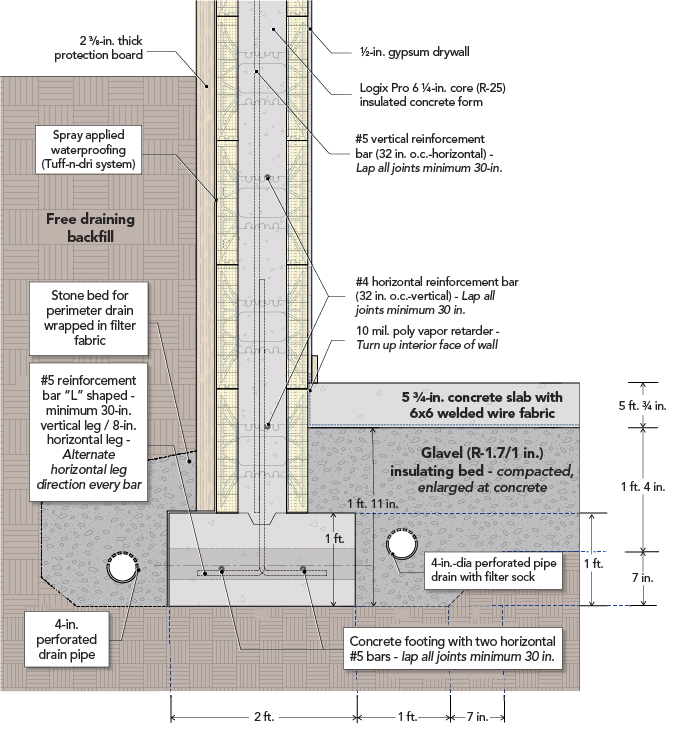
Here at Steven Baczek Architect, we regularly spec 10-in.-thick, steel-reinforced concrete foundation walls, but some projects call for deviation from our norm. This detail is from a house for which we went with a Logix Pro insulated concrete form (ICF) block foundation. One of the benefits of an ICF assembly is that insulation is integrated; the thermal resistance of this 11-3/4-in.-wide block with 6-1/4-in. core is R-25. Also, compared to our standard 10-in. foundation wall this system uses 38% less concrete, which is in line with reducing embodied carbon in our buildings. We have found, too, that ICFs are no harder to work with than the materials that go into our typical assembly.
Because this is a basement wall, groundwater management is critical. Although the 2-3/4-in. expanded polystyrene foam (EPS) that flanks the block walls is hydrophobic and the concrete core is continuous, we added Tremco’s Tuff-n-Dri spray-applied waterproofing to the exterior of the ICF blocks, as well as the exterior face of the footings.
We are confident that the waterproofing product will keep water out but to ensure that, it needed to be protected against the backfill stage of construction. We installed a 2-3/8-in.-thick vertically oriented rigid protection board, which also supports drainage. It reaches down to the top of the footing, helping to move water away from the foundation via a 4-in. perforated drainpipe at the exterior of the footing.
Together the protection board, perimeter drain, and free-draining backfill provide a “down and out” strategy to direct ground water away from the foundation before it challenges the waterproofing membrane, which is the final barrier to water intrusion.
A second perimeter drain sits to the inside of the foundation wall. Here we did something a little different, using a bed of insulating…
Weekly Newsletter
Get building science and energy efficiency advice, plus special offers, in your inbox.
This article is only available to GBA Prime Members
Sign up for a free trial and get instant access to this article as well as GBA’s complete library of premium articles and construction details.
Start Free TrialAlready a member? Log in
20 Comments
What is the protection board made of?
stolzberg,
It's a fiberglass product, which is often light pink, or yellow as seen in the wild. In Steve's video with Matt Risinger you can see the building they're talking about in this article, and I think it'll become self explanatory. It's not meant to be open above grade, and it only incidentally provides any R value - its primary purpose is to redirect the water down the fibers into the gravel.
https://www.youtube.com/watch?v=qIbBAqaSAck
thanks.
I'm not sure it's fair to compare the concrete used in a "standard 10" foundation wall", and that in an ICF foundation. There is nothing inherently stronger about ICF, so the standard wall could also be engineered to be 6" wide.
@Malcom, could you elaborate a bit on this?
To clarify my understanding of that part of the article, In Ontario, "Standard 10" foundation wall" is concrete with no rebar. They compensate for lack of rebar by building ticker wall. Only reason ICF can go down to 6" or 8" (depending on the soil type and hight) is because of rebar.
It escapes me why would anyone build a foundation wall without rebar but there it comes good old "everyone does it, or this is how it's done".
If "Standard 10" foundation wall" was build with the same amount rebar as ICF, I agree there is absolutely no difference and it could go down to 6 or 8".
boban,
ICF are basically a concrete structure that uses foam forms which are left in place. If they can use a 6" core, so can a conventionally formed concrete foundation. Most codes have prescriptive minimums for the width of concrete foundation walls. ICF structures don't have to follow those because they have been engineered. The same could be done with any concrete foundation.
Edit to respond to your clarification:
Our discussion stems from the detail being labelled as helping reduce concrete. So I guess you could argue that choosing to use ICF does that over an un-reinforced wall, although my point is that it really isn't a fair comparator when you have the option of simply adding the same rebar to reduce the width of the 10" one.
That still leaves the house with a 5 3/4" slab - which similarly could have been thinned out with a bit of steel added. Both situations begging the question as to whether there are any meaningful reductions there.
This series is interesting, but I wish Steven or Alexandra Baczek would respond to the questions and comments. So much of the value of GBA comes from the discussion, and I think this series would be greatly improved if there was a little back and forth on each of the articles!
Brendan,
I brought that up earlier in the series without much success. People look at details like this on GBA and see them as definitive good practice. They would benefit from some discussion to reassure them that is the case.
I agree and have encouraged Alexandra do this, but her availability seems very limited. That said, I understand the value of the expert's response and will follow up on this request.
Is 5 3/4" a "standard" thicknes for a basement slab?
I was curious as to why such an odd dimension was specified as well. I doubt any concrete crew has ever been required to pour exactly 5 3/4".
5-3/4" does seem odd, I can only imagine it was to hit a floor height design. There is another home that is ICCF with foamed glass floor insulation but no slab, which I thought was quite interesting. Any thoughts on slabless vs slab in this discussion?
I've got opinions on it, like everyone else.
I think the time required to truly level a granular surface, such that the top surface is both flat and level, would cost more and still be fussier than a well designed concrete slab with a good aggregate gradation, minimized cement content, shrinkage fibers, and additives to make it easy to place and finish. It doesn't even need to be all that thick- 3" is plenty and easy enough to place, smooth, and finish in ~ 4 hours.
Concrete can also be repaired to essentially a new state, should a section of it ever need removed.
I've got 2 comments: Steve mentions spraying the waterproofing on the exterior of the ICF and down onto the exterior faces of the footing. He doesn't show any capillary break between the footing and the concrete foundation wall. So there will be some moisture wicking up from the footings to the concrete, and some potential for moisture migration outward from the foundation to the interior. EPS foam is not a vapor barrier, so that doesn't help much. Small risk for sure, but spraying the waterproofing on top of the footing before the walls are set would eliminate this pathway at low incremental cost.
Second, IMVHO, 16"+ of Glavel for R-27 seems to be a bit of overkill, even for a cold climate. I'd probably go with 12" for a cold climate, and 6"-8" for a warmer one. Although I guess if this is Passive House construction, the R-27 might be required by the standard.
It does seem like a lot of excavation for R27, when 6" of EPS could realistically provide the same R value.
In the Build Show video he mentions they were excavating that deep anyway since it is a walk out on one side.
superman22x,
How would that affect the depth of the excavation necessary under the slab?
My understanding was they wanted the footings buried that deep on the walkout side, so they excavated the whole area to the same depth. But I'm not sure...
I think the Build Show youtube series is cool, and I really like what Steve does in particular. However, I am always slightly skeptical of the practicality of the methods sometimes because of how much product sponsorship there is.
superman22x,
I think the confusion may come from the drawing, which shows the excavation at one height under the slab, and another under the footings. The dimensioning seems to indicate this was a deliberate choice.
“[Deleted]”
Log in or become a member to post a comment.
Sign up Log in